- Absorption and dissipation of compressive stress
- Formation of a reliable “deformation seam” in cast iron parts, such as cylinder liners, diesel engine heads, or vessels subjected to thermal loads
- Redistribution of tensile load from areas of fatigue failure
- Maintaining original alignment and preserving the original surface structure – the absence of heat prevents deformation
- In most cases, the repair can be carried out at the customer’s site with minimal disassembly or without disassembly of the equipment, saving time and money
CTI
BAUFLEX AI (Artificial Intelligence)
Metal Stitching or the "Metalock" Method
Cold Repair of Cracks and Breaks in Cast Iron Structures
BAUFLEX offers its services for the restoration of industrial equipment using the Metalock technology. Metal stitching or the “Metalock” method is a simple yet effective way to repair cracked cast iron parts without welding. Cold repair of any cracks and breaks in structures made of cast iron, cast steel, or aluminum. Typically, structural damage occurs due to excessive load, accidents, improper use of equipment, or casting defects.
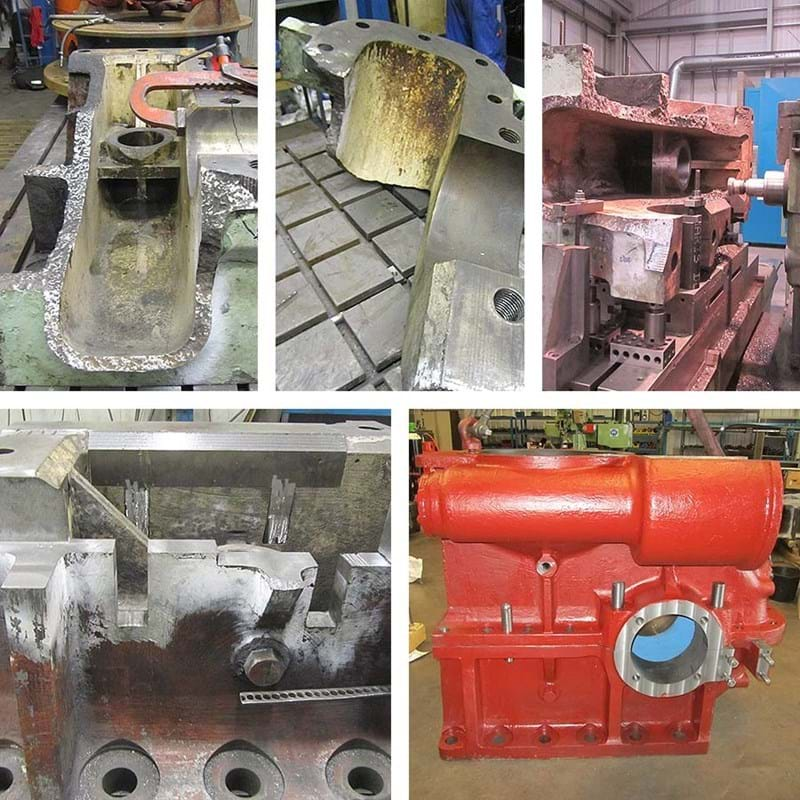
Proven Method for Repairing Machines and Structures
This repair method is proven and repeatedly tested, yet each application is unique, as every enterprise and the equipment used therein is unique. This feature is also inherent in ship engines, hydraulic presses, petrochemical equipment, old buildings, and historical structures.
More than 70 years ago, Metalock Engineering selected special tools, jigs, fixtures, and materials, and with their help developed a simple yet effective technology, which we today call the cold repair method and apply for the restoration of various objects – from factory equipment to historical structures.
Advantages of Metalock Metal Stitching:
- Application of this method at the customer’s site, 24/7 availability of our services, and the high qualification of Metalock specialists trained in our workshops.
- Less downtime – faster restoration of equipment to working condition.
- This procedure is a globally recognized repair method and is certified according to Lloyd’s Register requirements, certificate No. MNDE/REP/0017/06.
- Cold repair requires less expenditure than purchasing new cast iron parts.
Here are just some advantages of the “Metalock” technology:
Repair Process Using the “Metalock” Method:
- 1. After conducting the investigation, we prepare a report and present it to the client to obtain permission to carry out the repair. The part is then properly positioned, aligned, and secured with clamps and other fasteners.
- 2. Using a special jig, rows of holes are drilled along the fracture line to a depth corresponding to the depth of the working tool used.
- 3. The bridges between the holes are removed with a pneumatic chisel so that the resulting slot matches the shape of the “Metalock” keys.
- 4. The keys are dumbbell-shaped fasteners made from extremely ductile alloys. We produce keys of different sizes, and the engineer cuts the key to the required length according to the type of fracture being repaired.
- 5. The keys are driven into the holes layer by layer, forming metal-to-metal joints, and as a result, they become almost one with the material of the part.
- 6. Holes are drilled along the fracture line, after which studs are screwed into them so that each subsequent stud enters the previous one; these actions create a sealed joint that restores the rigidity of the cast iron structure.
- 7. “Metalock” studs are an essential part of the “Metalock” process as pneumatic equipment is often used for the repair.
- 8. The studs are screwed into the part so that their heads protrude slightly above the surface of the part, then the remaining irregularities are removed with a pneumatic chisel.
- 9. The surface of the repaired part is ground.
- 10. At the end of the procedure, a lacquer coating is applied to the part.